GRI 2–22
Sustainability at Swatch Group
Responsible operations, responsible corporate governance and sustainability are fundamentals for us and have been an integral part of our philosophy and corporate culture for many decades. We remain true to our vision and approach. Social responsibility, ethics and environmental protection have always been deeply anchored in our corporate culture. Swatch Group is committed to reducing energy consumption, minimizing its contribution to global warming, and using sustainable materials. The company enforces a zero-tolerance policy on corruption, modern slavery, and child labor. Swatch Group positions itself as an attractive and responsible employer and as a training company. Its business model is geared toward sustainable and long-term success.
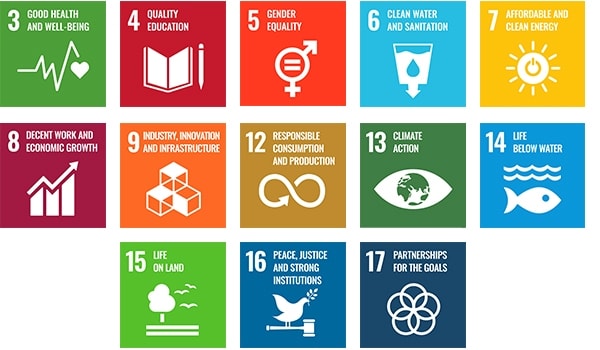
In 2024, the sustainability committees of our various companies focused on strengthening the integration of sustainability into corporate culture, directly involving key departments in sustainability thinking and actions. In order to engage all employees and raise their awareness, Swatch Group has also brought in an online training course on environmental issues. More than 1000 employees took the training within the first two months of the program starting.
In addition, workshops to define the next steps and goals on the path to sustainability were organized and held. Our Sustainability Report 2024 takes stock of all the measures implemented to date and presents the goals we have set ourselves for the next few years.
For example, we are updating our materiality analysis in accordance with the principle of double materiality. This assessment, which was made under the direction of the Sustainability department with the involvement of people from all the Group’s divisions, will enable us to adapt our sustainability strategy and goals in 2025. We continue to focus on Scope 3 in order to increase the effectiveness of the measures and further reduce these emissions. With the same aim in mind, we are also improving supply chain analysis in order to optimally meet our due diligence and transparency obligations.
We continue to invest in sustainability with passion, commitment and conviction, factoring in the entire life cycle and customer-oriented development of our products and the supply chain in all areas.
Since 2021, Swatch Group has published a sustainability report in line with GRI requirements in order to make reporting as transparent, comparable and comprehensive as possible. Swatch Group is also guided by the UN’s Sustainable Development Goals (SDGs) and, as a responsible company, makes a contribution to achieving these goals.
Sustainability Steering Committee
↗ Download the 2024 Sustainability Report
↗ Download the 2023 Sustainability Report
↗ Download the 2022 Sustainability Report
↗ Download the 2021 Sustainability Report
Contact
The Swatch Group LTD
P.O. Box 1232
CH-2501 Biel / Bienne